Just 18 months after Airbus declared its ambition to bring a zero-emissions aircraft into service by 2035, a critical development in that timeline has taken place around the engine that could take this aircraft to the air, reports Mark Pilling. In a transatlantic press conference, Airbus announced the signing of a partnership agreement with CFM International, a 50/50 joint venture between the engine giants GE and Safran Aircraft Engines, to collaborate on a hydrogen engine demonstration programme that will take flight around the middle of this decade. The programme’s objective is to perform ground and flight tests on a direct combustion engine fuelled by hydrogen, in preparation for entry-into-service of a zero-emission aircraft by 2035. The demonstration will use the very first Airbus A380 – MSN 1 – as a flying testbed equipped with liquid hydrogen tanks prepared at Airbus facilities in France and Germany. Airbus will also define the hydrogen propulsion system requirements, oversee flight testing and provide the A380 platform to test the hydrogen combustion engine in cruise phase, as well as measure condensation trails.
Under the ZEROe demonstrator programme, CFM will modify the combustor, fuel system and control system of a GE Passport turbofan to run on hydrogen. The engine, which is assembled in the US, was selected because of its physical size, advanced turbo machinery and fuel flow capability. It will be mounted along the rear fuselage of the flying testbed on a stub support to allow engine emissions, including contrails, to be monitored separately from those of the engines powering the aircraft. CFM will undertake an extensive ground test programme ahead of the A380 flight test.
The A380 will be fitted with four hermetically-sealed liquid hydrogen fuel tanks in the rear of the fuselage delivered from the Airbus Zero Emissions Development Centres, which are working on metallic hydrogen tanks, said Sabine Klauke, Chief Technical Officer at Airbus. The fuel load will consist of 400kg of liquid hydrogen. A new cryogenic fuel distribution system, including a new pump, seals and pipes will be required for this engine with the liquid hydrogen converted into a gas before combustion. There will also be cockpit modifications to monitor and manage the propulsion system.
“This is the most significant step undertaken at Airbus to usher in a new era of hydrogen-powered flight since the unveiling of our ZEROe concepts back in September 2020,” said Klauke. “By leveraging the expertise of American and European engine manufacturers to make progress on hydrogen combustion technology, this international partnership sends a clear message that our industry is committed to making zero-emission flight a reality.”
“Hydrogen combustion capability is one of the foundational technologies we are developing and maturing as part of the CFM RISE Program,” said Gaël Méheust, CEO of CFM. “Bringing together the collective capabilities and experience of CFM, our parent companies and Airbus, we really do have the dream team in place to successfully demonstrate a hydrogen propulsion system. We are deeply committed to helping the industry achieve the industry’s net carbon emissions goal that we have collectively set for ourselves through the Air Transport Action Group declaration last October. To achieve this goal, the industry needs to take action now – and we are.”
GE and Safran launched the technology demonstration programme RISE – Revolutionary Innovation for Sustainable Engines – in June 2021. It is aimed at developing open rotor powerplants that can be powered by 100% sustainable aviation fuel or liquid hydrogen for the next generation of single-aisle aircraft from 2035.
“Achieving sustainable aviation growth requires a holistic industry-wide approach. From the CFM perspective, we certainly support the broader use of sustainable aviation fuels – something the industry can do today to have a huge impact on its carbon footprint. Of course, this is in addition to building ever more fuel-efficient aircraft engines,” said Méheust.
“However, it is not the goal of our industry just to lower its carbon footprint, it is net zero carbon emissions and to achieve this we need to explore all the technology pathways at our disposal and hydrogen propulsion brings great promise. It is the true zero carbon emissions solution and at CFM it is one of the fundamental technologies we are developing and maturing as part of the RISE programme.”
Mohamed Ali, VP Engineering at GE Aviation, added: “CFM is now working with Airbus to make zero-emission aircraft a step closer to reality. Both GE and Safran, as parent companies of CFM, have experience with hydrogen fuel to power land-based gas turbines and rockets. This experience makes CFM the best-positioned engine maker to join the Airbus ZEROe programme.”
Explaining the challenges of hydrogen aircraft propulsion, he said: “For aircraft engine propulsion, to distribute the fuel from the storage tanks to the engine combustor, it will require the development of a new cryogenic fuel delivery system. Before the liquid hydrogen can enter the engine’s combustion chamber, we will need to convert it into gas to be burnt cleanly in the combustor. Unlike jet fuel, hydrogen is injected into the combustor as gas, so making its mixing with air actually easier. “
However, hydrogen burns at a much higher temperature than jet fuel, so CFM will need to build on its experience with advanced materials, coatings and cooling technology to develop combustor and turbine parts to withstand that temperature, and still achieve the same or better durability than what we have today, he said. Burning at a higher temperature also makes hydrogen susceptible to other emissions like nitrogen oxides and burns ten times faster than jet fuel, so requiring new technologies. For the programme, the liquid hydrogen will need to be stored at around minus 250°C in the four cryogenic fuel tanks and the liquid hydrogen converted into gas via a new technology heat exchanger.
“Is hydrogen harder? Yes. Is it doable? Absolutely,” said a confident Ali.
During the flight test phase, data will be gathered on the condensation trails produced by the engine in different atmospheric conditions, said Michel Brioude, Chief Technology Officer at Safran Aircraft Engines. “Hydrogen combustion does not emit CO2 but it does produce three times the amount of water, so condensation trails can contribute to the greenhouse effect and we will need to measure that,” he said. “Today, we don’t know how long they exist in the atmosphere.”
Klauke told the press event that the demonstration timeline announced was fitting exactly with the 2035 entry-into-service plan outlined at the Airbus Sustainability Summit in September 2020. The plan to conduct flight tests by the end of 2026 will enable Airbus to make technology choices for the aircraft’s propulsion system in 2027, she said.
Airbus Americas Chairman Jeff Knittel described the signing of the strategic partnership between Airbus and CFM as an historic day for aviation, adding: “Hydrogen propulsion is a fundamental part of the long-term solution and we are committed to this new aviation future.”
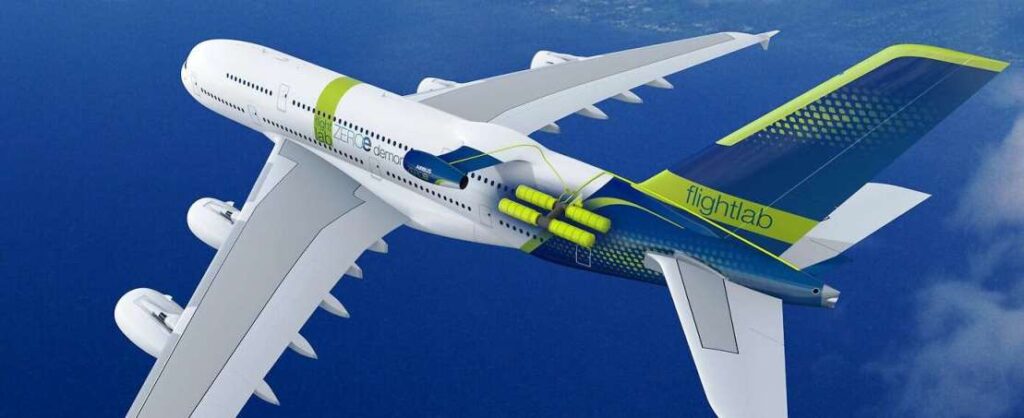
The Airbus A380 ZEROe demonstrator showing the four liquid hydrogen tanks and the GE Passport turbofan engine mounted on the rear fuselage (top and bottom images: Airbus)
Airbus, CFM, GE and Safran executives unveil their hydrogen propulsion partnership (starts 7:45)
Additional reporting by Christopher Surgenor
More News & Features
ZeroAvia attracts further support from American and new investment from Japan’s ITOCHU
Hydrogen aviation pioneer Universal Hydrogen fails, citing lack of funding
Fokker Next Gen partners with airBaltic on new liquid hydrogen powered commercial aircraft
Dovetail gets Australian state support and secures seaplane electric conversion deal from Norway
European aerospace supplier Aciturri takes key stake in Dovetail Electric Aviation
Inclusion of SAF in new climate legislation for EU cleantech industry welcomed by aviation sector